The Role of Phosphating Plants in Automotive Manufacturing
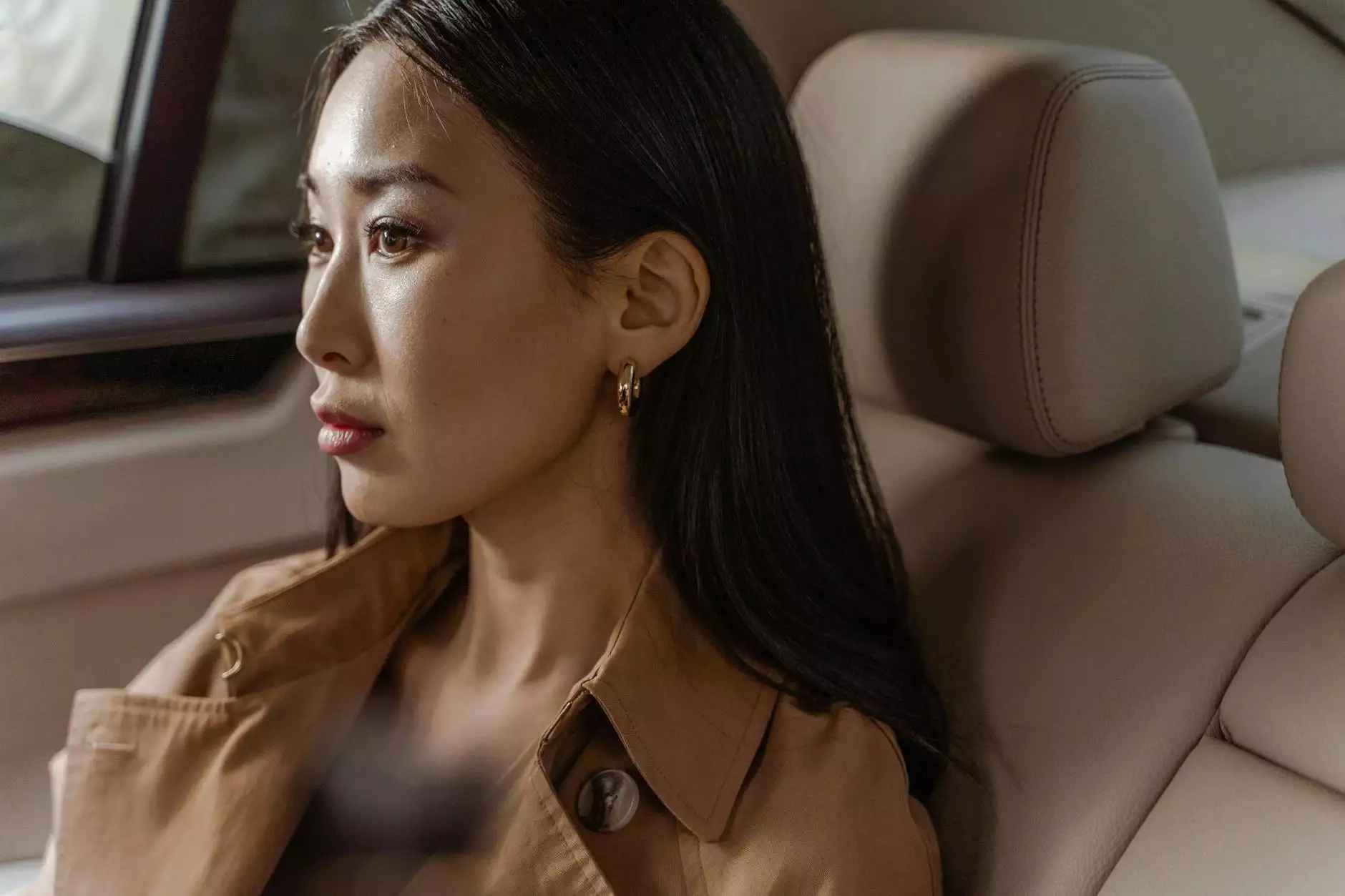
When it comes to the automotive industry, the finishing touches can make all the difference. Phosphating plants play a crucial role in ensuring that vehicles not only look appealing but also stand the test of time against the elements. In this article, we will delve deep into the functionalities, advantages, and significance of phosphating plants within the automotive sector.
What is a Phosphating Plant?
A phosphating plant is a specialized facility designed to apply a chemical conversion coating to metal surfaces, primarily iron and steel, to enhance their resistance to corrosion. This process typically involves the application of phosphoric acid, which reacts with the metal to create a protective layer that is essential for optimizing paint adhesion. This process is particularly valuable in automotive manufacturing, where durability and aesthetics are paramount.
How Phosphating Works
The phosphating process can be broken down into several key steps:
- Surface Preparation: The metal surfaces are thoroughly cleaned to remove oils, grease, and rust.
- Phosphating Treatment: The cleaned metals are immersed in a phosphating solution that contains phosphoric acid and metal phosphates. The chemical reaction creates a layer of insoluble phosphate crystals.
- Rinsing: After the phosphating process, the components are rinsed to remove any residual chemicals.
- Drying: The parts are dried to ensure no moisture remains, which could impact subsequent coating processes.
Benefits of Using a Phosphating Plant in Automotive Coating
The adoption of phosphating plants in automotive coating processes brings a plethora of benefits that enhance both performance and quality. Let’s explore some of these advantages:
1. Enhanced Corrosion Resistance
One of the primary functions of a phosphating treatment is to provide a robust barrier against corrosive elements. The phosphate layer significantly improves the corrosion resistance of steel, prolonging the life of automotive components and reducing maintenance costs.
2. Improved Paint Adhesion
Phosphating increases the surface area and creates a rough texture which improves the mechanical bond between the metal and paint. This enhances paint adhesion, ensuring that automotive finishes remain intact even under harsh environmental conditions.
3. Cost-Effectiveness
While implementing a phosphating plant requires an initial investment, the long-term cost savings are notable. By reducing the need for frequent repainting or repairs due to corrosion, manufacturers can see significant financial benefits over time.
4. Environmentally Friendly Process
Modern phosphating systems are designed to be environmentally sustainable. They use less hazardous materials and are more efficient, generating less waste compared to traditional coating methods.
Key Components of a Phosphating Plant
A well-designed phosphating plant consists of several key components that work together to ensure optimal performance:
- Treatment Tanks: These are where the phosphating solutions are held and where the metal parts undergo the phosphating process.
- Rinsing Stations: Essential for removing excess chemicals and preventing contamination of the phosphated layer.
- Drying Equipment: Used to eliminate moisture from the treated parts that could affect the subsequent finishing processes.
- Quality Control System: To monitor the efficacy of the phosphating process, ensuring that standards are consistently met.
Choosing the Right Phosphating Plant for Your Needs
When considering the implementation of a phosphating plant, it is essential to evaluate several factors:
- Capacity: Determine the volume of parts that need processing to choose a plant that meets your production requirements.
- Technology: Look for advanced phosphating solutions that offer efficiency, consistency, and low environmental impact.
- Vendor Reliability: Partner with a manufacturer that has a proven track record and offers robust support and maintenance services.
Implementing a Phosphating Process in Your Facility
Integrating a phosphating process into your existing production line can be challenging but rewarding. Here are essential steps to consider:
- Assessment: Conduct an assessment of your current processes to identify how phosphating can enhance your operations.
- Training: Invest in training your staff on handling chemicals and operating phosphating equipment safely.
- Testing: Before full implementation, conduct test runs to fine-tune the process and ensure quality standards are met.
Conclusion
The importance of phosphating plants in the automotive industry cannot be overstated. They not only provide enhanced corrosion protection and improved paint adhesion but also contribute significantly to the longevity and aesthetic quality of vehicles. As automotive technologies continue to advance, integrating these processes into manufacturing aligns with both industry standards and customer expectations.
For businesses looking to improve their coating processes and ensure quality finishes, investing in a phosphating plant represents a strategic move towards achieving excellence in automotive manufacturing. By understanding the nuances of the phosphating process and its benefits, manufacturers can unlock unprecedented efficiency and reliability in their production lines.
To learn more about phosphating plants and how they can enhance your automotive manufacturing processes, explore additional resources or connect with industry experts.