The Comprehensive Guide to Silicone Membranes for Vacuum Presses
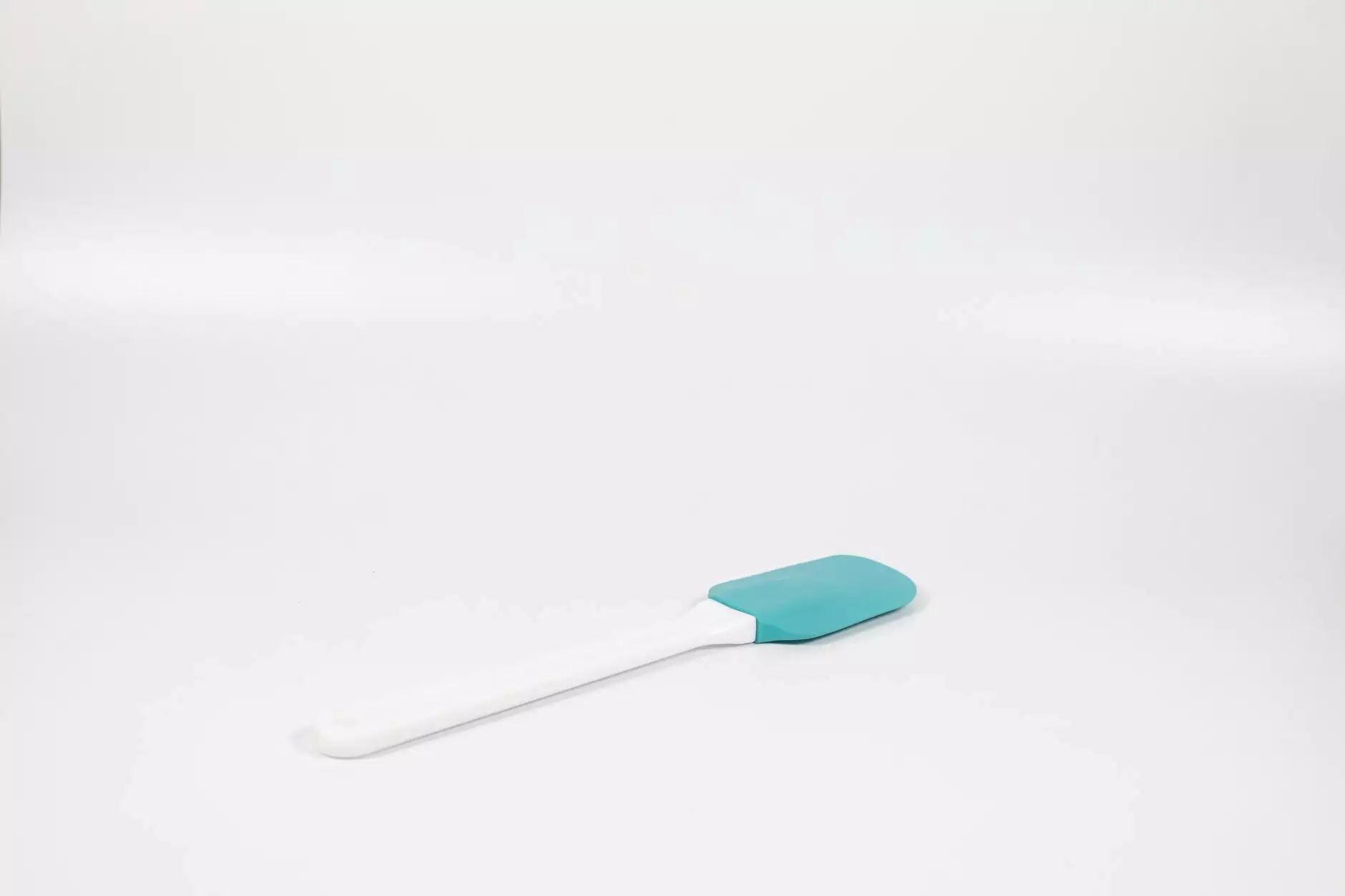
The world of vacuum presses is vast and intricate, offering numerous solutions across various industries. One such crucial component is the silicone membrane for vacuum press, which plays a vital role in ensuring efficient operations. This article dives deep into the specifics of silicone membranes, their significance, varied applications, and tips for selecting the ideal membrane for your vacuum pressing needs.
What is a Silicone Membrane?
A silicone membrane is a thin layer made from silicone rubber that is engineered to create a seal during the vacuum pressing process. Its properties make it uniquely qualified for high-performance tasks:
- Flexibility: Silicone membranes can easily conform to various shapes.
- Durability: Resistant to heat and degradation, these membranes can withstand extreme conditions.
- Non-stick surface: Ensures easy removal of materials post-pressing.
The Role of Silicone Membranes in Vacuum Presses
In vacuum pressing, the silicone membrane for vacuum press serves several critical functions:
- Sealing: Creates a tight seal that maintains a consistent vacuum level, essential for uniform pressure distribution.
- Protection: Shields the materials being pressed from potential contaminants and damage.
- Enhancing Quality: Helps in achieving high surface finishes and eliminates the risk of air pockets.
Advantages of Using Silicone Membranes
Choosing silicone membranes for your vacuum press comes with a plethora of advantages:
- Temperature Resistance: Silicone can handle a broad range of temperatures, making it suitable for various applications.
- Chemical Resistance: It is inherently resistant to many chemicals, minimizing degradation during use.
- Longevity: These membranes have an extended lifespan compared to traditional rubber membranes, leading to reduced replacement costs.
- Improved Performance: The consistent pressure exerted leads to better product quality and less waste.
Types of Membranes for Vacuum Presses
1. Silicone Membranes
Silicone membranes offer flexibility and resilience, making them ideal for a range of applications in woodworking, composites, and other manufacturing processes.
2. Rubber Membranes
While rubber membranes are less expensive, they may not deliver the same high-performance results as silicone. They can wear out more quickly and may not withstand extreme temperatures.
3. Natural Rubber Membranes
Natural rubber membranes provide good flexibility and resistance; however, they are less durable than silicone and can degrade over time if exposed to heat or harsh chemicals.
Choosing the Right Silicone Membrane for Your Vacuum Press
When selecting a silicone membrane for vacuum press, consider the following factors:
- Thickness: The thickness can impact the membrane's durability and performance. A thicker membrane can withstand more pressure but may also limit flexibility.
- Temperature Rating: Ensure the membrane can handle the specific temperature requirements of your application.
- Size and Shape: Choose a membrane that fits your press size and the shapes of the materials you'll be working with.
- Type of Materials Being Pressed: Consider the materials—such as wood, composites, and plastics—that you will be using and how the membranes will interact with them.
- Brand Reputation: Purchase from trusted manufacturers like vacuum-presses.com to ensure quality and reliability.
Maintenance and Care of Silicone Membranes
Proper maintenance can extend the life of your silicone membranes significantly:
- Cleaning: Regularly clean the membranes to remove any adhesive residues or materials that can create imperfections.
- Storage: Store silicone membranes flat in a cool, dry place away from direct sunlight to prevent deformation and damage.
- Inspection: Regularly inspect for any signs of wear, tear, or degradation and replace them promptly to ensure optimal performance.
The Impact of Quality on Vacuum System Performance
Investing in quality silicone membranes for vacuum presses is crucial for numerous reasons:
- Efficiency: High-quality membranes maintain vacuum levels efficiently, reducing energy consumption and improving production times.
- Cost Savings: Quality membranes reduce the need for frequent replacements, leading to lower long-term costs.
- Product Quality: They ensure that the end products meet industry standards and consumer expectations.
Conclusion
In summary, silicone membranes are an absolutely essential component of an effective vacuum press system. Their unique properties make them perfect for various applications, enhancing efficiency, product quality, and operational reliability. By choosing the right silicone membrane and maintaining it properly, businesses can significantly reduce costs while maximizing productivity. Visit vacuum-presses.com for a wide range of high-quality silicone membranes and related products to suit your vacuum pressing needs.
Frequently Asked Questions
What is the lifespan of a silicone membrane?
The lifespan can vary depending on usage and care, but high-quality silicone membranes can last for several years with proper maintenance.
Can silicone membranes be customized?
Yes, many manufacturers offer customization options to ensure a perfect fit for specific applications.
What makes silicone membranes superior to rubber membranes?
Silicone membranes usually offer better temperature resistance, durability, and performance compared to traditional rubber membranes.