The Importance of Injection Molding Tooling Design in Modern Manufacturing
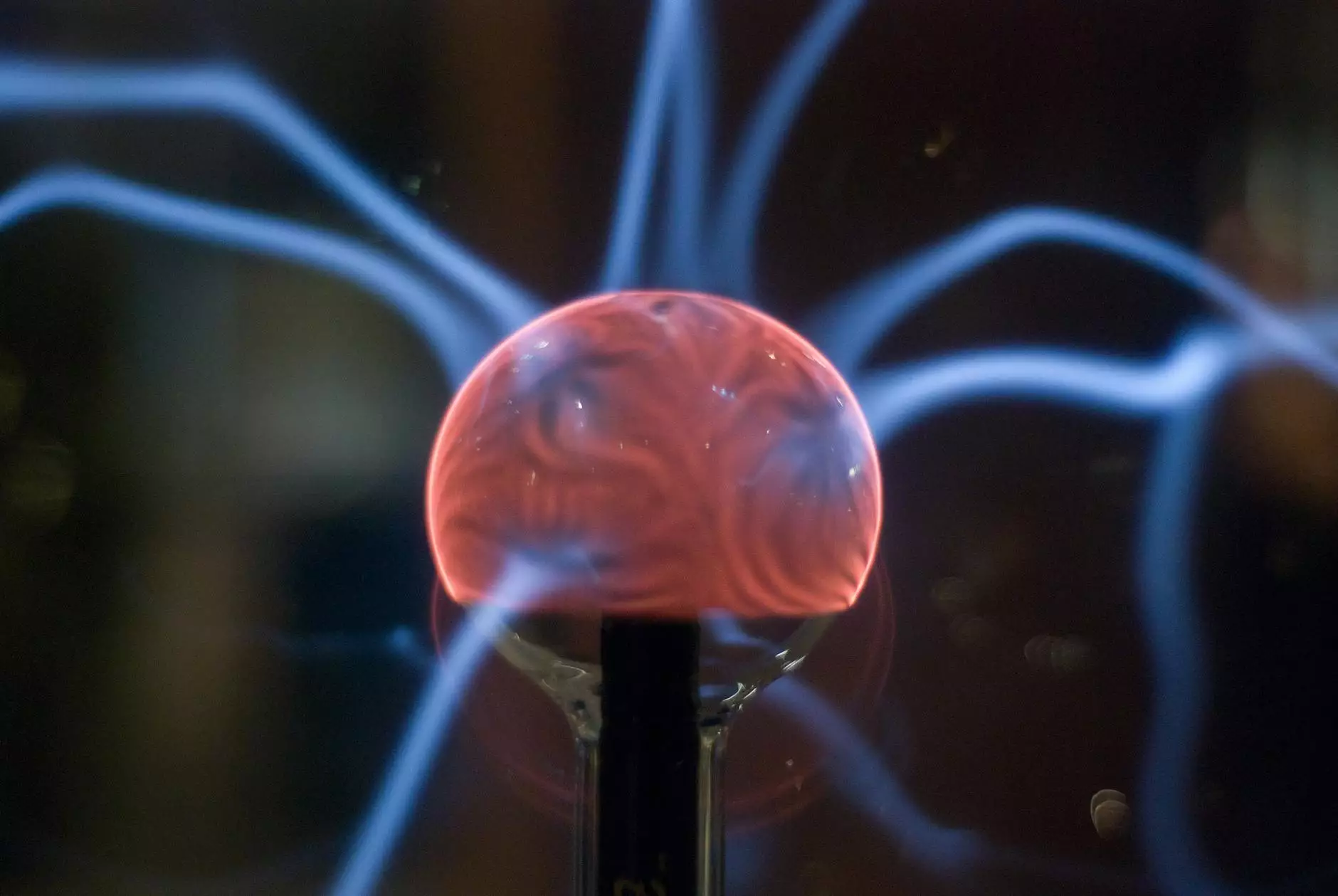
Injection molding tooling design stands as a cornerstone of contemporary manufacturing, particularly in industries reliant on the production of intricate plastic components. The process entails creating molds that are specifically tailored for mass manufacturing, enabling businesses to produce high-quality products with exceptional precision and efficiency.
Understanding Injection Molding
To grasp the significance of injection molding tooling design, it’s essential to first understand what injection molding is. This manufacturing process involves injecting molten material into a pre-designed mold to produce parts and components. The materials can vary widely, ranging from thermoplastics to thermosetting polymers. What makes injection molding particularly appealing is its ability to produce highly complex geometries with minimal waste, making it a preferred method in numerous sectors, including automotive, consumer electronics, and medical devices.
The Role of Tooling in Injection Molding
Tooling in injection molding refers to the creation and design of the mold used in the injection process. The success of injection molding largely hinges on the quality of tooling design, where precision, durability, and efficiency are paramount. Without the right tooling, even the best materials will not yield the desired outcomes. Here are some critical reasons why injection molding tooling design is vital:
- Accuracy: Proper tooling ensures that each part produced meets the specification requirements with high precision.
- Consistency: Well-designed molds allow for repeatable processes, producing identical parts in large quantities with minimal variation.
- Cost Efficiency: High-quality tooling can significantly reduce production costs by minimizing scrap and rework.
- Speed: Efficient tooling design allows for quicker turnover in production cycles, providing a competitive edge in the market.
Key Components of Injection Molding Tooling Design
Effective injection molding tooling design encompasses various elements that contribute to the overall success of the manufacturing process. Understanding these components is crucial for fabricators:
1. Mold Materials
The choice of materials for molds is vital. Common choices include steel and aluminum, with each offering distinct advantages. Steel molds tend to be more durable and can withstand higher production volumes, whereas aluminum molds can be more cost-effective for lower volume runs.
2. Mold Design
Designing a mold involves considering factors such as part geometry, draft angles, and cooling circuits. An adept designer must ensure that the mold can efficiently cool to reinforce dimensional stability and avoid warping, while also facilitating easy part ejection.
3. Cooling Systems
Efficient cooling is a critical aspect of tooling design. The cooling system must be designed to rapidly cool the injected material to solidify it while minimizing cycle times, thus improving production speed and efficiency.
4. Ejection System
The ejection system is responsible for removing the finished part from the mold. A well-designed ejection system minimizes the risk of damage to the part and can significantly reduce cycle time, which is an essential factor in high-volume production.
Challenges in Injection Molding Tooling Design
Despite its myriad benefits, injection molding tooling design is not without challenges. Some common difficulties include:
- Complex Part Geometries: As product designs become more intricate, the tooling must be equally sophisticated to ensure functionality.
- Material Limitations: Different materials react differently during the injection process, posing challenges in achieving optimal results.
- Time Constraints: The demand for faster turnaround times can pressure designers and fabricators, potentially compromising quality.
Advancements in Injection Molding Tooling Technology
Technological innovations continually influence injection molding tooling design. Some advancements include:
1. 3D Printing
3D printing technology is revolutionizing mold design and prototyping. It allows for rapid iterations and modifications, reducing the traditional lead time associated with creating molds.
2. CAD Software
Computer-Aided Design (CAD) software has transformed how molds are designed. Advanced software enables designers to create detailed and accurate models, allowing for simulations that predict mold performance and potential issues.
3. Smart Manufacturing
Integrating IoT (Internet of Things) technologies within the injection molding process helps monitor production in real-time, improving efficiency and reducing waste.
Choosing the Right Fabricator for Injection Molding Tooling Design
Selecting the right partner for injection molding tooling design is crucial for success. When considering fabricators, look for:
- Experience: Seek out companies with a proven track record in high-quality mold design and manufacturing.
- Technological Capabilities: Evaluate the technology they utilize, including design software and manufacturing techniques.
- Custom Solutions: Opt for fabricators who offer tailored solutions that cater to your specific needs and requirements.
- Support Services: A good fabricator should offer comprehensive support, from design through to post-production services.
The Future of Injection Molding Tooling Design
The future of injection molding tooling design holds exciting prospects. As industries continue to evolve, so too will the tools and technologies that drive them. Key focus areas include:
- Sustainability: Efforts to create environmentally friendly materials and processes will likely dominate future designs.
- Increased Automation: Automation in factories will streamline the production process, reducing labor costs and time.
- Integration of AI: Artificial Intelligence could play a crucial role in predictive maintenance and efficient design processes.
Conclusion
In summary, injection molding tooling design is a critical factor in the efficiency and effectiveness of modern manufacturing. Experts in the field, such as those at DeepMould.net, illustrate the importance of high-quality tooling and the profound impact it has on product quality, production speed, and cost efficiency. By investing in advanced tooling design and considering the challenges and opportunities within the field, businesses can ensure their place in the ever-evolving manufacturing landscape.
The relationship between tooling design and successful outcomes cannot be overstated, and as we look to the future, the continual advancements in technology will further enhance the capabilities of injection molding, paving the way for innovative designs and sustainable production practices.